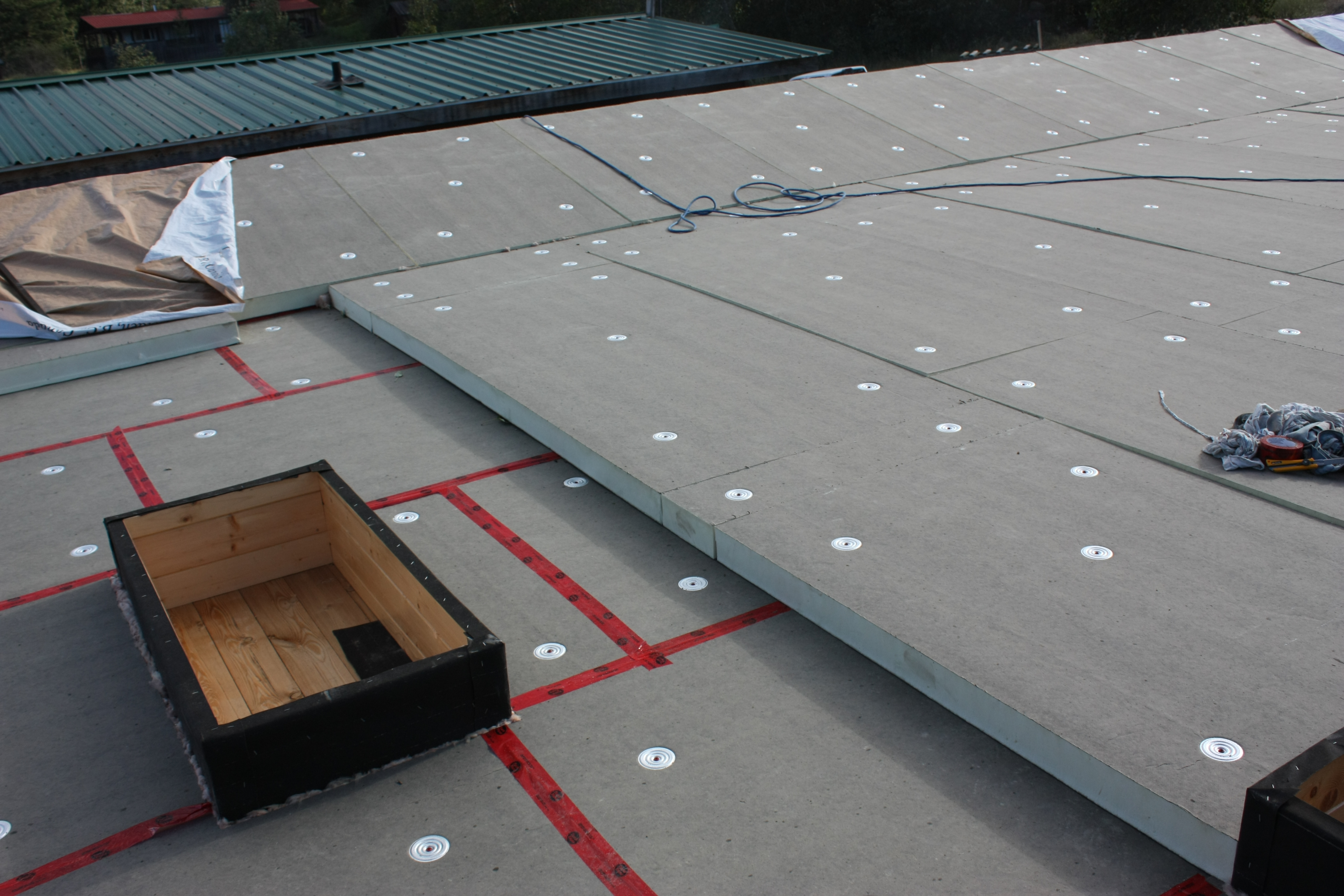
Finishing the roof has seemed like an exhausting and never-ending experience … the good news is that it is raining tonight (very good because BC is tinder dry), and the inside of the building is still dry! We will see in the morning if we have any leaks.
Two weeks ago we started the process of finishing the roof by laying 30# roofing felt. This actually made the roof kind of waterproof, but it still leaked around the skylights.
After the roofing felt we placed a double layer of rigid insulation on the roof deck. The insulation is a 4″ x 4′ x 8′ Firestone product rated at R25 (With two layers of insulation we have R50 for the roof insulation … the other roofing components will also add a little insulation). We staggered the layout pattern of the two layers so that none of the seams on one layer matched those on the other layer (or came within six inches of each other). The reason for this is simple. If the seams of the two layers line up it is possible that warm moist air from the building will reach the roof membrane and condense, creating moisture and the potential for rot and mildew in the roof assembly. We also taped all of the joints on the first layer of insulation. This tape was not called for, but I thought it was prudent. We mechanically attached each layer of the rigid insulation to the roof deck using five 5″ screws for the bottom layer and eight 9″ screws for the top layer. We used a large diameter washer with the screws, otherwise the screws punch through the insulation. The 9″ screws actually started life as 10″ screws (all of these items are Firestone products), but the tip of a 10″ screw would have wound up 1/2″ below the ceiling (not attractive) so we cut 1″ off the tip of these screws. We still got the recommended 1″ penetration into our roof deck, and we did not have to try and hit a rafter every time we placed a screw. We fitted the insulation tightly around the skylights and then stuffed any voids next to the skylights with rigid insulation. Handling this insulation was not fun, the outer surfaces have fibreglass in them and you go to bed feeling like someone has covered you in itching powder (even after a shower).
When we were done laying the rigid insulation we placed a double layer of 6 mil poly around the perimeter of the insulation to act as a moisture barrier between the ground and the rigid insulation. This poly lapped the double layer of dow rigid insulation (R24) already placed around the top of the wall (this dow insulation is approved for ground burial). Ideally we would have simply extended the dow insulation up to the top of the roof insulation but we placed and backfilled this insulation first and this was no longer an option (the dow insulation forms the thermal wrap around the back of the building). We then had Alvin come in and he backfilled around the back wall flush to the top of the roof insulation.
After Alvin was done backfilling we placed a double layer of 6 mil poly that lapped the roof and extends down the backfilled berm for ten feet. We stapled the poly to the roof insulation. This poly acts as a moisture barrier and keeps water from the back wall. We then placed a 3′ wide strip of epdm half on and half off the back edge of the roof. This rubber protects the roof membrane where it goes off the roof onto the berm. We adhered the epdm to the insulation using the appropriate Firestone adhesive. This began our love affair with the various Firestone solvents and adhesives. I hope I am not addicted, and now fully appreciate the expression ‘as mad as a hatter’! We also cut cants for the skylights which are 4″ higher than the top of the insulation. I made the cants from the roof insulation by cutting it at 45 degrees through the table saw and beveling the joints.
At this point we were ready to start laying the 45 mil EPDM roof membrane! David and Melanie (Sandra’s brother and sister-in-law) came out and helped for a day and Mike (who was out helping last year) was back this year and helped us for a week on the roof. Thanks everybody! I bought the EPDM in four 10’x100′ rolls and figured we would lay continuous rows for the roof. We placed our first row above the greenhouse (about 74′ long), folded it back on itself, and started applying adhesive to the upper half of the membrane and to the insulation underneath it. After about twenty feet Sandra suggested we place what we had glued and we quickly realized we were in trouble; 74′ of EPDM is heavy, we were not able to smoothly lay the EPDM out, the EPDM quickly folded over on itself and stuck together because of the adhesive. It was like trying to pull a length of sticky tape apart after it has folded over itself, except you risk being suffocated as you lie buried in 10′ of EPDM. It was not a pretty sight, the language was coarse and it took a good half hour to get the EPDM straightened out. As an added bonus it was a hot day and unless you wore gloves the EPDM was too hot to handle. I can also report that the adhesive is wonderful for body hair removal. Somewhat deflated after two hours of struggling with the EPDM we decided to split each row into three sections of EPDM lapped at the joints a minimum of six inches and overhanging the roof on each side by two feet. After that point the job proceeded fairly smoothly over the next couple of days. This also made it much simpler to place the EPDM over the skylights and cut the required openings.
After the last row of EPDM was placed at the bottom of the roof we installed the water collection canals at the bottom of the U’s. The canals are simply 3’x8′ metal flashing painted with tar on the bottom and brown paint on the top to prevent rusting. These canals will not be covered by the final berm and they channel water off of the roof to cisterns (when we get around to installing them). We used 9″ screws and washers to attach the canals to the roof deck.
We then experienced the black Firestone solvent used to bond two EPDM seams together (we are sitting down so we do not wander off the roof). As stated earlier we lapped the vertical seams six inches and we lapped rows by a foot. My hope is that even if the seal between seams fails that the roof slope and the overlap will act to keep water on top of the membrane and not work under it.
After this we caulked all the seams. This Firestone product was actually fairly benign. We found it useful to warm the tubes of caulking slightly with a heat gun. It flowed better and was easier to place.
Finally, we flashed the corners of all of the skylights. We cut the flashing into 12″ diameter circles and molded it to the outside corners of the skylights. The flashing was fairly easy to install, but again the primer applied underneath the flashing was strong.
Installing the EPDM roof was a challenging process, but we are happy with the end result. We will see if any leaks are evident after the first heavy rain! We learned as we went and I imagine an experienced installer would laugh at our adventure.
I am tired just typing this out!
On Monday Alvin is back and we will do the final roof berm …
PS – Mike took a number of these pictures. Thanks Mike.
Reading about your adventures as you undertake a better life for you and your family is inspiring and exciting! I hope to be following in your Earthship building shoes one year soon!
Keep up the great work and frequent posts!
First off I would like to say that your site is just wonderful. My wife and I want to build an earth shelter home and the earthship concept has really taken hold on us. We live in central texas and the summer temp. is between 96f-105f. My concern is that the thermal mass will not be enough to cool our house off. Would it be best to creat an atic to run ducting for a centralized AC unit? What is your take on the extream heat issues that we face every summer all summer?
I think you would be surprised by how cool the house would be on its own. I think Earthship Biotecture recently finished building one in Texeas…perhaps you could get better answers from them? http://www.earthship.com Our issue is different; how to keep warm all winter. 🙂
hi any advice on a roll-out-able membrane that can be laid in a box gutter and up the sides in a continuous surface to stop leaks? I am DIY and I think I have seen something somewhere that is laid out then using a heat gun is then waterproof? Any suggestions appreciated. Cheers M
We have not actually done anything yet like you propose. I think as soon as we get to the planters we will be considering this. If you come up with any brainwaves in the meantime, please share!